In the near future, as you drive your car and sing along to your favourite radio channel, the road surface beneath your car could be working hard to mitigate the negative effects of both noise, emissions and microplastics from the tyres.
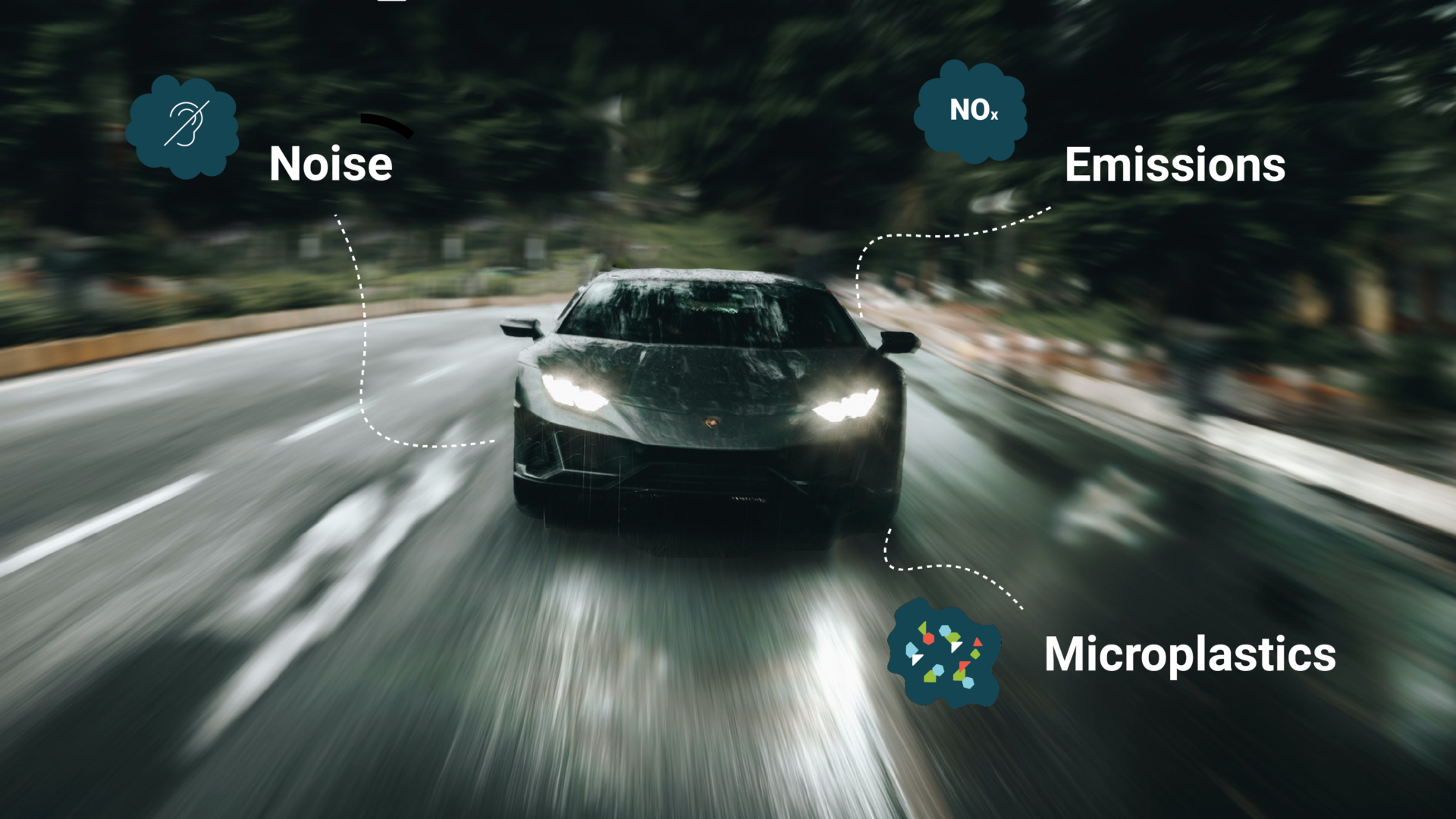
While some of the NEMO partners are busy developing the remote-sensing technology that will enable the monitoring of actual emissions and noise in European cities, others are focusing on developing cutting edge mitigating technologies. A team of researchers from the GITECO research group at the University of Cantabria in Spain, and M+P noise and vibration consultants, are designing an innovative mix of materials for road surfaces, that will have the capacity to counter three of the main negative effects from transport.
A large share of noise from traffic comes from the contact between the tyre and pavement, while conventional pavement surfaces and the wear of car tyres significantly contributes to the flow of microplastics into the ocean. The novel asphalt mixtures developed in the NEMO project are designed to reduce rolling noise while minimizing rolling resistance, as well as to study the potential collection of microplastics in the asphalt layer pore network minimizing the runoff into the oceans.
Friction free particle collection
Car tyres release particles through mechanical friction that contributes significantly to the flow of microplastics into the environment. Due to the lack of water collection and treatment systems in roads close to, but outside, urban areas, these contaminants are often left uncontrolled. It is estimated that the amount of tyre wear makes up 5-10% of the total amount of plastics that end up in the oceans. It has also been estimated that up to 95% of microplastics could potentially be collected and stored within the multiple layers of a new and more innovative porous asphalt mixture.
As urban roads are already designed to handle and treat water runoff, the priority in these areas is not to deal with microplastics but to enable the reduction of harmful emissions, like NOx, and noise.
Originally developed to prevent skidding on wet pavements in the thirties in the US, porous asphalt was ready for general applications on highways and airports in the seventies. This was also the basis for the European development of porous asphalt in the early eighties, based on the research at the University of Cantabria where a mix-design method for porous asphalt was established. In 1985 the operational use on motorways and major roads began and a rapid development took place especially when the noise reducing benefits was recognised.
A catalyst for reducing air
The winning new formulas are currently being investigated by the research team, with the main objective of achieving a superior noise reduction over a long lifetime, while keeping a low rolling resistance to reduce vehicle’s fume emissions. The peri-urban design is based on a double layer construction due to their known superior noise reduction and to the expectations concerning their potential capacity to store microplastics within the pore network. All these considerations will naturally also have to be made without compromising on the mechanical performance of the road surface.
Photocatalytic materials exhibit air purifying properties and gets activated by sunlight, enabling degradation of pollutants from the surroundings and transformation to less harmful products. It has shown to be a promising technique to reduce a number of air contaminants, especially at sites with a high level of pollution: highly trafficked roads, tunnels, etc. The research team is evaluating which photocatalytic material is the most efficient to be selected for its final integration to the surface layer.
Test driving in the laboratory
Road surface technology has become increasingly research-heavy and multi-purposed, yet also highly standardised and protocol based. NEMO’s new designs therefore go through gruelling tests to comply with the various standards for road surfaces, both European (EN) and International (ISO), and while considering various available protocols for the testing itself. NEMO will also develop new laboratory protocols, such as how to quantify the retained microplastics on the porous asphalt.
Knowledge gained in previous research projects, such as FORESEE and SAFER-UP, is also helping to speed up the development of the new designs.
The research team at the University of Cantabria is now finalizing the new designs for the urban and peri-urban mixes, including the selection and methodology for the incorporation of photocatalytic materials. Finally, the GITECO research group is developing a standard protocol for the generation and collection of microplastics both at the laboratory and in the field. Once these tasks are completed, the next steps are, on the one hand, to test both designs on the pavement fatigue carrousel of IFSTTAR in France, and on the other hand, to produce and built in Florence a full-scaled pilot road section with the designed urban mixture.
If you’re interested in learning more about NEMO’s work with mitigation solutions, please contact Irune Indacoechea, R&D project manager, University of Cantabria.
irune.indacoechea@unican.es